Вибродиагностика
Содержание
Статьи о вибродиагностике
Вибродиагностика – это технология обнаружения дефектов и неисправностей в работающих машинах и оборудовании по вибрации. Кроме вибрации могут использоваться и другие процессы в работающих объектах диагностики, наиболее информативный – силовой ток электропривода.
В технологию вибродиагностики могут входить определение места, вида и величины (степени опасности) каждого из дефектов, а также прогноз их развития и оценка остаточного ресурса объекта (до предаварийного состояния, без учета возможных восстановительных работ). Наибольшее развитие получила вибродиагностика машин и оборудования с узлами вращения (вращающегося оборудования).
По способу формирования анализируемой вибрации объекта во время диагностирования принято выделять два направления вибродиагностики вращающегося оборудования. Первое - функциональная вибродиагностика без вмешательства в работу объекта (Condition monitoring), второе - тестовая вибродиагностика с исследованием реакции вибрации объекта на тестовое воздействие, например, внешний удар, сброс – наброс нагрузки и т.п. (такую диагностику принято относить к вибрационному методу неразрушающего контроля).
Есть еще и специальное направление вибродиагностики вращающегося оборудования – на стендах, на которых из-за трудностей в обеспечении типовых режимов работы объекта вибродиагностика проводится в нештатных режимах вращения. Обычно диагностику оборудования на стендах относят к более широкому направлению функциональной диагностики.
В функциональную вибродиагностику вращающегося оборудования входят три основных вида диагностики:
-
оперативная диагностика опасных дефектов (онлайн диагностика) по результатам мониторинга состояния, т.е. по факту регистрации изменений состояния
-
вибродиагностика зарождающихся дефектов (периодическая), с поиском дефектов до момента регистрации изменений состояния,
-
диагностика виброотказов (превышений вибрацией объекта установленных на нее норм) с определением их причин.
Последний вид вибродиагностики – составная часть технологии виброналадки, обеспечивающей поддержание вибрации эксплуатируемого объекта в пределах установленных норм. Как правило, значительный вклад в решение задач виброналадки вносит и тестовая вибродиагностика.
По условиям участия специалиста в процессе диагностирования можно выделить три основных направления диагностики. Первое – экспертная диагностика, когда все основные операции по анализу получаемой информации и принятию решения выполняет специалист с диагностической подготовкой. Второе – автоматизированная диагностика, когда анализ информации и постановка предварительного диагноза производятся автоматически, но специалист контролирует (с возможностью коррекции) и промежуточные операции, и результат диагностирования. Третье – автоматическая диагностика - не требует участия специалиста ни в одной операции диагностирования после запуска системы диагностики на объекте.
И, наконец, перед вибродиагностикой могут ставиться разные цели, но основных - две:
-
внедрение и развитие технологий обслуживания и ремонта вращающегося оборудования по фактическому состоянию,
-
внедрение и развитие технологий управления вращающимся оборудованием по текущему состоянию.
Главные задачи вибродиагностики, решаемые для достижения первой цели – обнаружение типовых дефектов на ранней стадии развития и долгосрочный прогноз безотказной работы объекта, главные задачи, решаемые для достижения второй цели – обнаружение любых опасных дефектов практически мгновенно и прогноз остаточного ресурса объекта с такими дефектами.
Подготовка специалистов по вибродиагностике вращающегося оборудования
Минимальный срок подготовки после освоения основ вибромониторинга – 36 часов, 3 уровня подготовки с практическим освоением средств и программ вибродиагностики вращающегося оборудования:
-
начальный, с изучением особенностей диагностических измерений и анализа вибрации машин роторного типа, диагностических признаков разных дефектов, а также с освоением технических средств и программ автоматической диагностики,
-
расширенный с изучением основ обнаружения дефектов на ранней стадии развития, освоением методик, технических средств и программного обеспечения для диагностики дефектов в установившемся режиме работы вращающегося оборудования,
-
полный, с дополнительным освоением технологий проведения диагностических обследований, диагностики причин виброотказов, а также методов и систем диагностики дефектов в режиме онлайн
Программы обучения
Заявка на обучение
Индивидуальные консультации по методикам и техническим средствам вибродиагностики вращающегося оборудования, как по однократным измерениям, так и по результатам мониторинга, подбор переносных, мобильных и стационарных средств вибродиагностики.
Особенности вибродиагностики вращающегося оборудования
Возможности и используемые методы вибродиагностики вращающегося оборудования во многом зависят от типа объекта диагностики и режимов его работы. По типам объектов они определяются наличием или отсутствием узлов возвратно-поступательного действия, а по режимам работы – количеством часто используемых режимов в процессе эксплуатации объекта и длительностью интервалов работы на тех из них, которые выбираются для диагностики,
В вибродиагностике вращающегося оборудования без узлов возвратно-поступательного действия одним из главных критериев появления дефектов является обнаружение ударов, особенно микроударов, создающих импульсные компоненты в сигнале вибрации. Самые эффективные методы обнаружения периодических ударов – различные виды спектрального анализа вибрации с накоплением результатов, непериодических ударов – анализ изменений формы сигнала или его мощности во времени.
На рис. 7.1. приведены спектры виброскорости и виброускорения агрегата в одной из стандартных точек контроля на подшипниковом узле. Спектр виброскорости используется для контроля наиболее мощных составляющих вибрации с частотой до 1000Гц, спектр виброускорения – для получения диагностической информации, содержащейся в более высокочастотных составляющих вибрации. Приведенное на втором графике в линейном масштабе изображение спектра затрудняет его графический анализ, поэтому спектры виброускорения чаще отображаются в логарифмическом масштабе по оси амплитуд (в децибелах, дБ), как это показано на третьем графике.
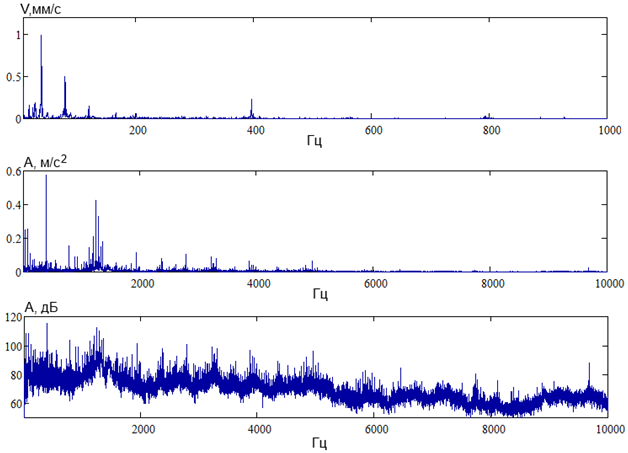
Рис.7.1. Спектр виброскорости в стандартном диапазоне частот, спектр виброускорения в расширенном диапазоне частот (линейный масштаб по оси амплитуд) и тот же спектр в децибелах виброускорения.
Вибрация, возбуждаемая короткими ударными импульсами, мало изменяет ее спектр, лишь незначительно повышая уровень случайных составляющих в широком диапазоне частот. Обнаруживаются ударные импульсы по форме высокочастотной вибрации, как это показано на первом графике рис.7.2. Более наглядной и удобной для дальнейшей обработки является форма огибающей высокочастотной вибрации, отражающая изменения ее мощности во времени и показанная на втором графике. Если удары периодические, как это видно по форме огибающей, можно продолжить анализ высокочастотной вибрации, взяв спектр огибающей, показанный на третьем графике. На состав спектра огибающей высокочастотной вибрации влияют и частоты следования ударов, а их может быть несколько, и форма удара, и зависимость силы удара от времени. Поэтому информация, получаемая при анализе формы и спектров огибающей высокочастотной вибрации, измеренной в разных точках агрегата, дает возможность определять и вид дефекта, приводящего к появлению ударов, и место его возникновения, и степень его опасности.
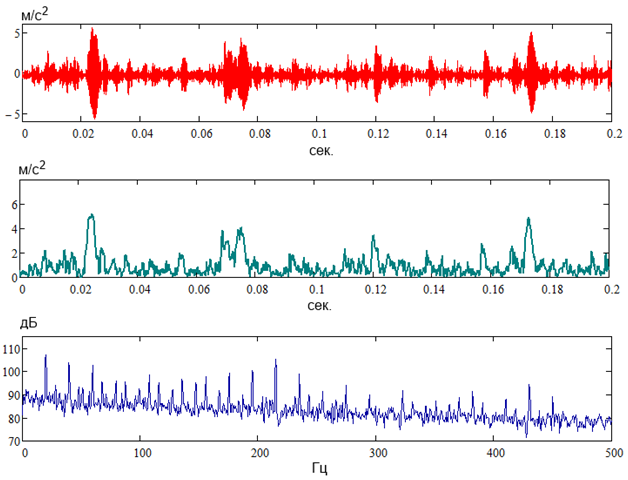
Рис.7.2. Форма сигнала вибрации на выходе широкополосного фильтра 1,6 – 6,0 кГц (первый график), форма ее огибающей (второй график) и спектр огибающей (третий график)
Измерение спектров сигнала вибрации, включая низкие и средние частоты, а также пиковых значений и спектров огибающей высокочастотной вибрации, на каждой опоре вращения роторной машины позволяет обнаружить большинство видов дефектов до того, как они станут опасными.
В агрегатах с крупными узлами возвратно-поступательного действия, например, поршневого типа, мощные удары – неотъемлемая составляющая их функционирования. Ту часть дефектов, которая изменяет мощность периодических ударов в таких агрегатах, можно обнаружить с помощью спектрального анализа вибрации. Однако основная часть дефектов возвратно-поступательных узлов обнаруживается по результатам сравнения формы и интервалов в группе последовательных импульсов вибрации и/или давления, поэтому для решения такой задачи основным средством анализа вибрации становится не анализатор спектра, а осциллограф. Необходимо также учитывать, что для обнаружения дефектов узлов вращения в таких агрегатах методы обнаружения вибрации, создаваемой микроударами (на фоне сильных ударов) не подходят, и приходится переходить к другим, чаще всего косвенными или невибрационным методам диагностирования узлов вращения.
Особенности диагностики зарождающихся дефектов
Колебательные силы, возбуждаемые дефектом на этапе зарождения, настолько малы, что не изменяют уровень низкочастотной вибрации, измеряемой по действующим стандартам, ни в одной из точек ее контроля. Изменяется лишь часть параметров отдельных составляющих вибрации, как правило, на высоких частотах, вплоть до ультразвуковых. Эти составляющие, как правило, могут быть выделены из сигнала вибрации лишь в точках контроля, близко расположенных к месту приложения колебательных сил. Обнаружить такие изменения можно при условии стабильности основных компонент вибрации, т.е. на установившемся режиме работы агрегата, в тех точках, где реакция контролируемых составляющих вибрации на зарождающийся дефект максимальна.
Таким образом, диагностика зарождающихся дефектов требует измерения и анализа вибрации в широком диапазоне частот, в большом числе точек контроля, с выбором оптимального направления измерения и на установившемся режиме работы объекта диагностики. Поскольку развитие зарождающихся дефектов идет медленно, интервалы между измерениями могут быть большими и их можно проводить последовательно с использованием переносных средств измерения вибрации, а анализ результатов и постановку диагноза выполнять в лабораторных условиях.
Одно из важных направлений развития диагностики зарождающихся дефектов – увеличение числа точек и направлений контроля преимущественно высокочастотной вибрации. Такие измерения можно проводить на корпусе и трубопроводах агрегатов с жидкой или газообразной рабочей средой, получая большой объем диагностической информации об особенностях пульсаций давления в рабочей среде. Можно также выбирать дополнительные точки и направления контроля вибрации на корпусе агрегата, наиболее сильно реагирующие на появление пульсирующих (крутящих) моментов сил, действующих как на ротор, так и на корпус агрегата.
В переносных системах вибродиагностики часто используются диагностические признаки с максимальной чувствительностью к зарождающимся дефектам, получаемые, например, из спектров огибающей высокочастотной и ультразвуковой вибрации. Такие признаки упрощают решение задач автоматизации диагностики. Однако по мере роста дефекта эти методы часто снижают чувствительность к дефекту, поэтому параллельно с ними применяются и дополнительные признаки развитых дефектов. Но для эффективного использования признаков сильных дефектов необходимо одновременно измерять вибрацию в нескольких точках контроля, в которых эти дефекты существенно изменяют параметры вибрации.
В системах диагностики на основе одно-двухканальных виброанализаторов реализовать такие измерения практически невозможно. Поэтому при появлении развитых дефектов в одних узлах агрегата, в других узлах автоматизированная программа диагностики, в которую не заложены признаки удаленных дефектов, обнаруживает неидентифицированные дефекты. Их идентифицировать приходится вручную, т.е. от оператора, работающего с переносной системой вибродиагностики, для уточнения вида сильных дефектов требуется диагностическая подготовка, особенно, если диагностика производится впервые, т.е. нет истории длительных наблюдений за развитием дефекта с момента зарождения.
Естественно, что переносные системы автоматизированной диагностики постоянно развиваются, и одним из перспективных направлений такого развития является использование многоканальных переносных или мобильных виброанализаторов для полной диагностики опасных дефектов, в том числе в режимах пуска и скачка нагрузки, по однократным измерениям вибрации без анализа истории их развития от момента зарождения.
Особенности оперативной (онлайн) диагностики опасных дефектов
Оперативная диагностика может быть реализована только при параллельном измерении и анализе вибрации во всех требуемых для диагностики точках контроля, а в случае дополнительного использования параметров других процессов – при их измерении и анализе параллельно с вибрацией. Для этого применяются многоканальные онлайн анализаторы процессов, в первую очередь, вибрации и тока с максимальной скоростью реакции на изменение состояния вращающегося оборудования.
Основным требованием к оперативной диагностике является ее быстродействие при высокой достоверности диагноза. Однако задачи обеспечения высокой скорости получения, достоверности и глубины диагноза находятся в противоречии, необходим компромиссный подход при их совместном решении. Первым шагом при таком компромиссе является переход на обнаружение дефектов не с момента зарождения, а с того момента, когда дефект начинает реально влиять на состояние объекта, т.е. диагностику проводят либо после регистрации изменения состояния, либо периодически, но лишь тогда, когда объект не находится в бездефектном состоянии. А для того, чтобы обнаружить слабые дефекты, вводятся дополнительные, более низкие и адаптируемые пороги. При этом для минимизации вероятности ложного срабатывания в средства обнаружения вводят алгоритмы накопления решений, наиболее частым из которых является тройное подряд подтверждение факта перехода объекта в состояние с дефектами.
Каковы же предельные скорости онлайн диагностики вращающегося оборудования по вибрации? Многолетний опыт регистрации скачкообразных изменений состояния по вибрации показал, что принять обоснованное решение можно при накоплении и анализе вибрации в течение трех оборотов ротора с момента скачка. Но для снижения вероятности ложного срабатывания рекомендуется тройное подтверждение факта скачка состояния, т.е. минимальное время достоверного обнаружения скачка соответствует девяти периодам вращения ротора (плюс время обработки информации). Учитывая тот факт, что скачек состояния связан, прежде всего, с возбуждением широкополосной вибрации ударного происхождения, результаты измерения такой вибрации становятся некоррелированными в два раза быстрее, поэтому тройное подтверждение скачка состояние потребуется время, равное 6 периодам вращения ротора.
Типовое время накопления информации для диагностики причины изменения состояния при явно выраженных дефектах, как показывает опыт, в три раза больше, и при тройном подтверждении диагноза близко к 20 периодам вращения ротора. Учитывая тот факт, что современная цифровая обработка сигналов вибрации проводится параллельно измерениям и практически не влияет на скорость выработки решения, приведенные данные о минимальном времени накопления информации для обнаружения и идентификации типовых дефектов во вращающемся оборудовании можно использовать на практике.
Как пример можно привести данные о скорости обнаружения изменений состояния и идентификации ее причины (для типовых дефектов) в автоматической системе оперативной диагностики СМД-4, см раздел «Средства вибродиагностики». Для агрегатов с частотой вращения ротора 50Гц и выше оно составляет ½ секунды, что обеспечивает возможность использования таких систем для управления работой агрегата по текущему состоянию.
Оперативная диагностика разрабатывается, в основном, для использования в стационарных системах мониторинга и диагностики, и оптимальным решением для таких систем является их объединение с системами автоматического управления. В таком случае к ней могут предъявляться дополнительные требования – прогноз остаточного ресурса при появлении развивающихся дефектов и автономная работа системы во время ее эксплуатации (без участия человека).
Особенности диагностики виброотказов
Диагностика причин повышенной вибрации работающего агрегата – один из самых сложных видов диагностики, если его проводить без вывода агрегата из работы. Основная причина – отсутствие, как правило, априорной информации об изменениях вибрационного состояния, получаемых по «истории» измерений или из группового вибрационного «портрета», создаваемого при анализе вибрации группы идентичных агрегатов. Недостаток информации не позволяет автоматизировать диагностику виброотказов, а эксперты компенсируют недостаток информации анализом вибрации и других процессов в специальных «тестовых» режимах работы агрегата. А поскольку тестовые режимы – составная часть работ по виброналадке агрегатов, особенности диагностики виброотказов вращающегося оборудования рассматриваются в разделе «Виброналадка».
Важной особенностью любого из указанных видов вибродиагностики вращающегося оборудования является и ее дополнение невибрационными методами, позволяющими внешними средствами «видеть» колебательные процессы или вызывающие их колебательные силы внутри агрегатов. Наиболее информативный их таких методов – анализ тока электропривода агрегата, в котором проявляются и колебания ротора электрической машины относительно статора, и пульсирующие моменты, действующие на ротор электродвигателя через муфту из-за пульсаций величины нагрузки.
Следует также отметить, что диагностика разных узлов вращающегося оборудования имеет свою существенную специфику, поэтому, как правило, более глубокое рассмотрение особенностей вибродиагностики проводится индивидуально для типовых узлов вращающегося оборудования, с учетом свойств формируемых в них колебательных сил. Так, индивидуальному рассмотрению подлежит:
-
вибродиагностика ротора и соединенных муфтами роторов в собственных опорах вращения,
-
вибродиагностика подшипников качения,
-
вибродиагностика подшипников скольжения и гибких роторов в подшипниках скольжения,
-
вибродиагностика механических передач,
-
вибродиагностика рабочих колес, работающих в жидких средах, например, насосов,
-
вибродиагностика рабочих колес, работающих в газовых средах, например, турбин,
-
вибродиагностика электромагнитной системы электрических машин разных типов,
-
вибродиагностика цилиндропоршневой группы (совместно с коленчатым и распред валами)
Вибродиагностика других узлов вращающегося оборудования, являющихся источником колебательных сил и вибрации, как и диагностика корпусных и фундаментных конструкций по передаваемой через них вибрации других узлов работающего оборудования, не рассматривается без привязки к конкретному агрегату. Соответственно, методика диагностирования или заменяющее ее диагностическое программное обеспечение должны адаптироваться к каждому виду агрегатов.
Еще одной особенностью любого вида диагностики, в том числе и вибродиагностики, являются способы и правила построения порогов для разделения состояния объекта на разные зоны состояния по каждому из используемых диагностических параметров. В вибродиагностике общих правил нет, поэтому одной из задач разработки методик диагностирования конкретных объектов является определение или величин этих порогов, или правил их построения. Чаще всего для диагностики используются те же принципы построения порогов по накопленным значениям периодически измеряемых параметров вибрации и других процессов, что и в вибрационном мониторинге. Но поскольку для контролируемых параметров могут использоваться групповые пороги, отсчитываемые от среднего значения по группе идентичных агрегатов, а разброс этих значений может быть большим, то и устанавливаемые пороги по группе для каждого параметра должны превышать, как правило, двойную величину его среднеквадратичного отклонения от среднего значения для бездефектных агрегатов.
Кроме того в диагностике есть признаки, не используемые для мониторинга состояния по мощности конкретных составляющих вибрации и тока – это их амплитудная модуляция. В измеряемой вибрации модуляция гармонических составляющих с глубиной более 20% считается признаком появления развитого дефекта, в токе таким признаком обычно считается амплитудная модуляция основной составляющей с глубиной более 2%.
Наиболее сложно определяется порог состояния диагностируемого узла по амплитудной модуляции случайной вибрации, возбуждаемой силами трения сразу в нескольких поверхностях трения. Этот порог существенно зависит от вклада трения конкретных поверхностей в измеряемую на удалении случайную вибрацию и, как правило, устанавливается на основе экспериментальных исследований нескольких однотипных агрегатов.
Дополнительной особенностью вибродиагностики является значительная зависимость величин диагностических параметров от внешних условий, к которым относятся времена года, температура окружающей среды, неконтролируемые изменения режима работы объекта, и другие. Все это приводит к необходимости адаптации пороговых значений каждого параметра к естественным флуктуациям его величины.
Для Вашего удобства все статьи нашего сайта по теме «Вибродиагностика» мы собрали в одном месте.
Вы можете прочитать их в разделе Статьи о вибродиагностике
Содержание