Простейшая система мониторинга состояния машин и оборудования
У технической и медицинской диагностики общая цель – продлить полноценную жизнь подопечного настолько, насколько это возможно. А для этого надо решить две основные задачи – вовремя обнаруживать его болезни, чтобы их можно было вылечить, и подбирать условия жизни с учетом реального здоровья. Но есть и существенные различия. Главное – в технике существует экономическая целесообразность принятия решений, как о продлении жизненного цикла, так и о глубине необходимой диагностики. А частное – техника сама не скажет, что ей плохо, поэтому за ее состоянием надо следить.
Как следить за состоянием работающей техники? Автомобиль, например, можно доставить к специалисту. И если специалист оснащен современными системами диагностики, он за короткое время проведет диагностику и даст прогноз состояния на не очень далекое будущее – обычно, как и в медицине, на полгода, через которые можно диагностику повторить. И производительность специалиста будет высокая, и цены реальные, 0,1-0,5% от стоимости Вашего автомобиля. Следствие – технологии диагностики техники, которую легко доставить в центр диагностики и обслуживания, существуют и успешно развиваются.
Но есть другая ситуация, когда специалиста надо вызвать к объекту, да еще со всей системой диагностики, тогда и цены могут оказаться неподъемными, да и специалиста хорошего в Вашем регионе может и не быть. Как в такой ситуации обеспечивать диагностику техники, и нужна ли она вообще? В необходимости диагностики эксплуатируемой техники, после того как в последние годы резко выросла эффективность и снизились затраты на техническую диагностику, уже никто не сомневается. А вот оптимально организовать ее удается далеко не всем.
Если проанализировать многочисленные отказы техники, то причиной, по крайней мере, половины из них являются ошибочные действия человека. Но не каждый раз человек своими действиями сразу доводит технику до отказа, гораздо чаще, спохватившись, он исправляет свои ошибки и переводит режим ее работы в безопасный. Но что случилось за время работы в аварийноопасном режиме, и каким стало реальное состояние техники – обычно остается неизвестным. А ведь надо обязательно контролировать последствия работы техники в таком режиме, чтобы не допустить в дальнейшем аварии с катастрофическими результатами. Как правило, такой контроль оказывается даже более важным, чем контроль естественного износа техники.
На больших предприятиях, где техники много, часто создаются диагностические службы, сотрудники которых специализируются в диагностике разных видов технических систем и отвечают совместно с обслуживающим персоналом и ремонтными службами за поддержание их работоспособного состояния между крупными (средними и капитальными) ремонтами. Средние предприятия во многих странах часто не включают в свой штат диагностов, а заключают договоры на диагностическое обслуживание со специализированными диагностическими фирмами, чаще всего занимающимися авторизованным обслуживанием техники конкретных изготовителей. А что делать небольшим предприятиям, эксплуатирующим небольшое количество типовых механизмов, которые невозможно демонтировать для доставки на диагностику и обслуживание в специализированный центр, а ошибки при ее эксплуатации встречаются даже чаще, чем на крупных предприятиях с квалифицированным обслуживающим персоналом? Приглашать специалистов по диагностике после каждой такой ошибки это прямой путь к разорению.
В таких случаях можно пойти по тропе «народной» медицины. Нет врача – мы сами контролируем свое здоровье, для чего используем зрение, слух и несколько простейших приборов, например термометр, тонометр и т.п. А для определения причины ухудшения здоровья пользуемся медицинскими справочниками для неспециалистов, советами бывалых, или, в лучшем случае, телефонными консультациями врача, которому сообщаем результаты измерений, собственных ощущений и наблюдений. Именно таким же образом можно поступать и с техническими системами, лишь бы существовали недорогие измерительные приборы, доступные для освоения неподготовленным обслуживающим персоналом, и с выходными данными, существенно зависящими от состояния объекта контроля, а также соответствующий справочник начинающего диагноста. Тогда можно решить вопрос уменьшения аварийности хотя бы простейшей из эксплуатируемой техники без ненужных и затратных профилактических обслуживаний и ремонтов после каждой такой ошибки. Да и делать при необходимости небольшие ремонты несложной техники многие ее собственники научились, а контроль состояния даст возможность не делать лишнего. Только где взять такие приборы и справочники?
Два года назад Северо-Западный учебный центр поставил перед собой задачу поиска недорогой системы мониторинга состояния типовых машин и механизмов, надежность которых определяется, в основном, узлами трения, чтобы организовать краткосрочную специализированную подготовку по оценке последствий таких ошибок тех, кто такие системы имеет. А в результате поиска оказалось, что, несмотря на обилие диагностической аппаратуры, эффективной и недорогой системы мониторинга состояния, которую не надо привязывать к конструктивным особенностям и режимам работы объекта, нет. Не решить многих задач контроля состояния с помощью измерителя температуры, даже дистанционного (пирометра), с помощью виброметра, рассчитанного на контроль низкочастотной вибрации, или разрекламированного прибора для контроля состояния подшипников по ультразвуку. Вывод – даже при минимальных требованиях к качеству контроля состояния надо обращаться к экспертам, для которых выпускается огромная номенклатура сложных и дорогих средств диагностики – тепловизоров, анализаторов вибрации и смазки, давления и тока, а к ним – сложное программное обеспечение по мониторингу и диагностике.
Тогда и было принято руководством Ассоциации ВАСТ решение – собрать самые простые и эффективные решения по контролю состояния вращающегося оборудования, не требующие привязки к конкретному его виду, в одном приборе, а для накопления результатов периодических измерений с целью последующих консультаций со специалистами создать простейшую программу мониторинга состояния машин и оборудования. А затем предложить использовать эту систему на предприятиях с небольшим количеством эксплуатируемой техники в качестве первого шага в освоении средств мониторинга и диагностики.
Из вторичных процессов в работающих машинах и оборудовании было решено контролировать два вида – виброакустические и тепловые, отказавшись от тока (признаки основных дефектов, обнаруживаемых по току двигателя, есть и в сигнале вибрации), и смазки (признаки дефектов смазки есть в сигналах и вибрации, и температуры). Кроме того, продукты износа в смазке можно обнаруживать и визуально, просматривая накапливающиеся отложения в магнитных пробках, картере и т.п.
Наибольшие сложности были связаны с принятием решений в рамках мониторинга состояния по вибрации. Ведь разные дефекты, возникающие во вращающемся оборудовании, проявляют себя в вибрации и воздушном шуме на разных частотах, начиная от инфразвуковых и кончая ультразвуковыми. Именно поэтому эксперты в области виброакустической диагностики используют несколько видов измерительных датчиков, а при анализе сигнала разделяют его на тысячи разных по частоте компонент (составляющих), т.е. проводят его узкополосный спектральный анализ. Такая диагностика, требующая привязки к каждому виду объектов контроля, оказывается дорогостоящей и требует серьезной подготовки специалиста, поэтому был принят ряд решений по упрощению используемых в разрабатываемой системе мониторинга алгоритмов контроля состояния, но так, чтобы снижение вероятности пропуска наиболее опасных дефектов свести к минимуму.
Из принятых решений, реализуемых в новом измерительном приборе, следует выделить следующие:
1. Использование только одного пьезоэлектрического датчика виброускорения, работающего во всем диапазоне частот, от инфразвуковых 2Гц до ультразвуковых 25кГц.
2. Использование типовых алгоритмов контроля вибрации машин и оборудования, предусмотренных государственными стандартами.
3. Анализ сигнала вибрации с разделением не на тысячи составляющих разной частоты, а не более чем на 50.
4. Реализация алгоритма обнаружения дефектов смазки подшипников по ударным импульсам – источникам ультразвуковой вибрации.
5. Включение в состав прибора канала дистанционного измерения температуры объектов по инфракрасному излучению.
6. Сравнение результатов измерения с порогами сразу после окончания измерения непосредственно в приборе.
7. Использование оптического канала измерения частоты вращения роторов, необходимого для мониторинга вибрации многоскоростных машин,
8. Обеспечение возможности прослушивания измеряемой вибрации через наушники (режим стетоскопа).
Кроме перечисленных технических решений, для накопления данных измерений конкретных машин с их последующим анализом было решено обеспечить возможность измерения вибрации и температуры по маршрутам, создаваемым во внешней программе мониторинга и диагностики.
Для реализации перечисленных решений пришлось использовать весь арсенал возможностей цифровой техники, в том числе 24-разрядные аналого-цифровые преобразователи последних поколений, и разработать специальные алгоритмы подавления собственных шумов измерительной аппаратуры.
Из стандартных видов контроля вибрации реализованы измерения виброскорости и виброперемещения в полосах частот 2-1000Гц, 10-1000Гц и 10-2000Гц, для обнаружения изменений состояния с возможностью оценки в ряде случаев вида и величины опасных дефектов использован третьоктавный анализ виброускорения в частотном диапазоне 10-10000гц, а для низкооборотных машин - в диапазоне 2-10000Гц. Для контроля состояния смазки и раннего обнаружения некоторых видов дефектов подшипников качения известным методом ударных импульсов реализуется возможность измерения среднеквадратичного и пикового значений виброускорения на высоких частотах, а также специального параметра, наиболее полно реагирующего как на зарождающиеся, так и на развитые дефекты – их среднегеометрической величины.
Третьоктавный анализ вибрации выбран потому, что позволяет выделить по частоте наиболее сильные гармонические ряды в сигнале вибрации, а в каждом из рядов разделить первую и вторую гармоники. Прослушивание преобразованного в звук сигнала вибрации позволяет проводить, но только качественный, частотный анализ сигнала органами слуха, которые делят сигнал на более высокое количество частотных полос. Органы слуха позволяют разделить 7 (точнее 12) частотных составляющих (нот) в октаве, в то время как в третьоктавном спектре на одну октаву приходится только три полосы.
Разработку прибора ведут специалисты ООО «ВАСТ-АРП» и ООО «Вибротехника» под руководством А.В. Баркова. Созданы опытные образцы прибора, который, несмотря на дополнительные возможности, получил такое же название, как и простейшие приборы, измеряющие вибрацию - виброметр ВТ-21. Его внешний вид показан на рис.1.
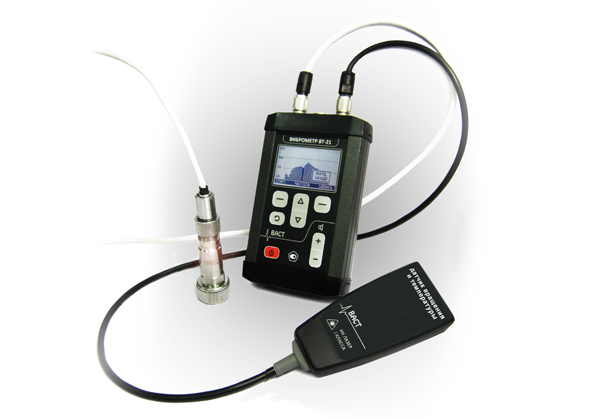
Рис.1. Виброметр ВТ-21
ВТ-21 может проводить любые из перечисленных видов измерений вибрации, температуры и частоты вращения и хранить результаты измерений в своей памяти без использования внешних программ. Однако для сравнения результатов измерений с порогами непосредственно в виброметре, эти пороги надо сформировать и ввести в прибор из внешней программы, устанавливаемой на компьютер.
Наиболее просто сформировать пороги на величину вибрации неподвижных узлов вращающегося оборудования только в стандартной полосе частот, обычно 2-1000Гц или 10-1000Гц. Они определены для разных видов оборудования действующими регламентами и стандартами. Кроме того, в документации производителя оборудования могут еще задаваться зоны допустимой частоты вращения и допустимой температуры отдельных узлов, но определить пороги на величину многочисленных составляющих вибрации эксплуатируемого оборудования может пользователь диагностической системы или эксперт после накопления базы данных с измерениями.
Существует два разных способа определения порогов на отдельные составляющие вибрации - по данным группы последовательных измерений этих составляющих вибрации, выполненных за длительное время эксплуатации конкретной машины, или по данным группы аналогичных измерений, выполненных у нескольких одинаковых машин без ограничений на длительность их эксплуатации. Работу по определению порогов рекомендуется выполнять на компьютере, воспользовавшись прикладной программой мониторинга состояния VibroM-21, в которой автоматизированы основные операции расчета и внесения порогов в прибор.
Программа мониторинга VibroM-21, главное окно которой приведено на рис.2, кроме сбора результатов измерений и определения пороговых значений выполняет еще несколько важных функций.
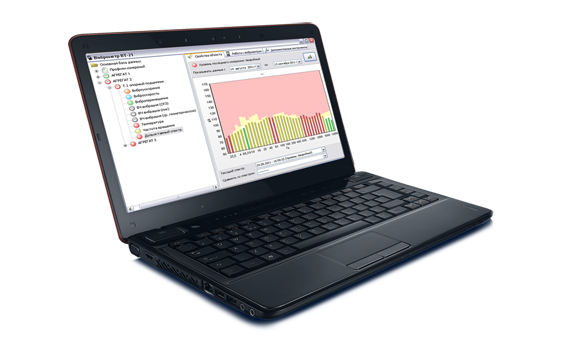
Рис.2. Программа VibroM-21
К основным функциям VibroM-21 относятся:
- составление маршрутов (заданий) измерений для каждой из точек контроля вибрации (температуры, частоты вращения) каждого из контролируемых объектов и передача их в виброметр,
- прием данных измерений из виброметра, хранение их в базе данных, сравнение результатов измерений с пороговыми значениями и вывод результатов,
- расчет и построение пороговых значений по результатам проведенных ранее измерений,
- построение и анализ трендов изменения состояния объектов и величины любого (выбранного из числа контролируемых) параметра измеряемых сигналов,
- контроль выполнения плановых измерений,
- контроль возможных ошибок оператора при проведении измерений (по третьоктавным спектрам),
- составление отчетов.
Изменение состояния объекта контроля обнаруживается в приборе (и, независимо, в программе) автоматически. Для этого при измерениях вибрации используются до четырех порогов, из которых два средних являются основными (порог «предупреждение» и порог «опасность»). Первый (нижний) порог служит для фиксации отсутствия измеряемого сигнала либо при ошибках измерения, либо при измерении вибрации остановленного оборудования. Верхний порог может устанавливаться для того, чтобы обнаруживать предаварийное состояние оборудования или ошибки измерений.
При автоматическом обнаружении изменения состояния по любому из контролируемых параметров (по превышению порога «предупреждение»), см рис 3 обеспечивается возможность формирования краткосрочного прогноза состояния - по трендам развития этого или любого другого с наметившейся тенденцией роста параметра как это показано на рис. 4.
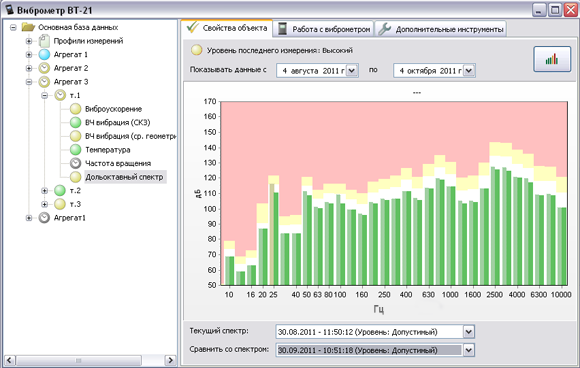
Рис.3. Обнаружение изменения состояния объекта по третьоктавному спектру вибрации. (Спектр с несколькими измерениями и порогами)
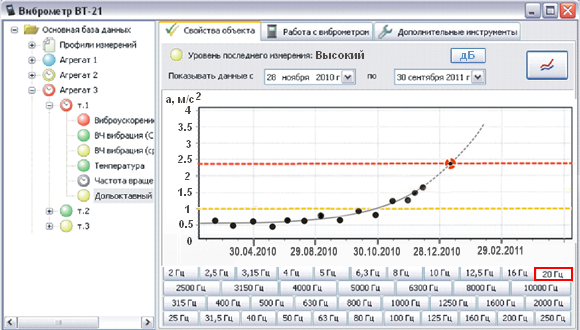
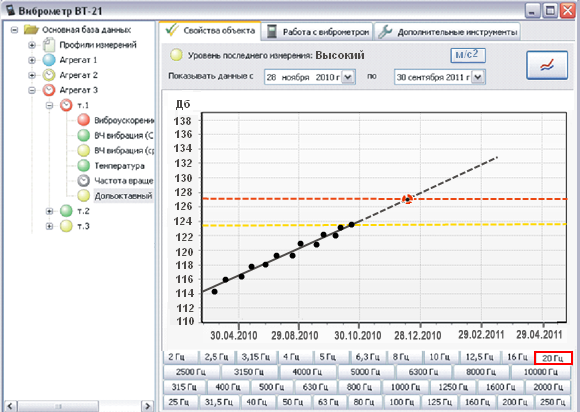
Рис.4 Прогнозирование состояния объекта по тренду изменения одной из составляющих вибрации, измеряемой в линейных (верхний рисунок) или в логарифмических (нижний рисунок) единицах.
Наиболее сложной задачей мониторинга состояния агрегата с использованием предлагаемой системы является оценка вида возникшей в результате ошибочных действий персонала неисправности. Решать эту задачу, хотя бы приблизительно, весьма важно, так как без ответа на вопрос, в чем заключается дефект и в каком узле агрегата он находится, невозможно определить, сколько еще времени может проработать агрегат до возможной аварии. В большинстве случаев для этого приходится приглашать эксперта с профессиональной системой диагностики. Но если его нет, можно попытаться дать приблизительную оценку вида, дефекта самостоятельно.
Для такой оценки необходимо определить группу тех из измеряемых параметров, которые изменились по сравнению с эталонным значением на величину большую, чем статистическая погрешность, и сравнить эту группу с группами, характеризующими различные дефекты. Список изменившихся параметров может выдать программа VibroM-21, а список параметров, характеризующих признаки основных дефектов агрегата, Вы можете составить сами, воспользовавшись разрабатываемой для этого инструкцией.
Как показывает практический опыт, имея информацию о частоте вращения и конструктивных характеристиках Вашего агрегата, составление такого списка не занимает много времени, а задача сравнения двух списков не является очень сложной.. Наиболее простой способ освоить простейшую систему идентификации обнаруживаемых дефектов - пройти двухдневное обучение в Северо-Западном учебном центре или у его представителей. Кроме того, можно получить квалифицированную помощь, обратившись по линиям связи к разработчикам системы.
В других материалах, размещенных на данном сайте, на основном сайте Ассоциации и в публикациях, на которые делаются ссылки, Вы можете получить более полную информацию о выпускаемых Ассоциацией ВАСТ системах контроля, мониторинга и диагностики работающих машин и механизмов.
За счет чего может быть получен основной экономический эффект от использования простейшей системы мониторинга состояния? Прежде всего, за счет повышения эффективности контроля состояния машин и оборудования обслуживающим их персоналом, одной из обязанностей которого и является контроль состояния, но без наличия диагностической подготовки и при использовании простейшего термометра и, иногда, виброметра такой контроль не может иметь высокую достоверность. Результат использования даже простейшей системы мониторинга очевиден – сокращение количества аварийных остановок машин и оборудования. Второй источник экономического эффекта – повышение качества взаимодействия со службой диагностики, если таковая есть на предприятии или заключен договор с внешним диагностическим центром. Хорошо известно, что кроме плановых диагностических измерений службе диагностики около трети выездов на диагностируемые объекты приходится делать по экстренным вызовам обслуживающего персонала. При наличии у персонала простейших систем мониторинга состояния большинство таких вызовов перестают быть срочными, они могут планироваться. Да и качество диагностики при использовании собранной обслуживающим персоналом истории изменений вибрации и температуры объектов мониторинга несомненно растет.